Introducing Granite AGS™ Parkson’s Aerated Granular Sludge system!
Introducing Granite AGS™ Parkson’s Aerated Granular Sludge system!
Parkson recently launched the Granite AGS™ process, a new and innovative method for biological treatment utilizing densified activated sludge. Granite AGS™ is a fill-and-draw granular sludge process that operates in a batch mode. Granular sludge particles contain multiple layers of microbes. The outer layers typically contain aerobic microbes that have access to surrounding dissolved oxygen during the aerated portion of the cycle. Inner layers are typically anaerobic and anoxic microbes that achieve Bio-P uptake and removal of nitrite and nitrate. The layered bacteria allow available carbon to be shared between microbes, eliminating, or reducing chemical addition needed for nutrient removal.
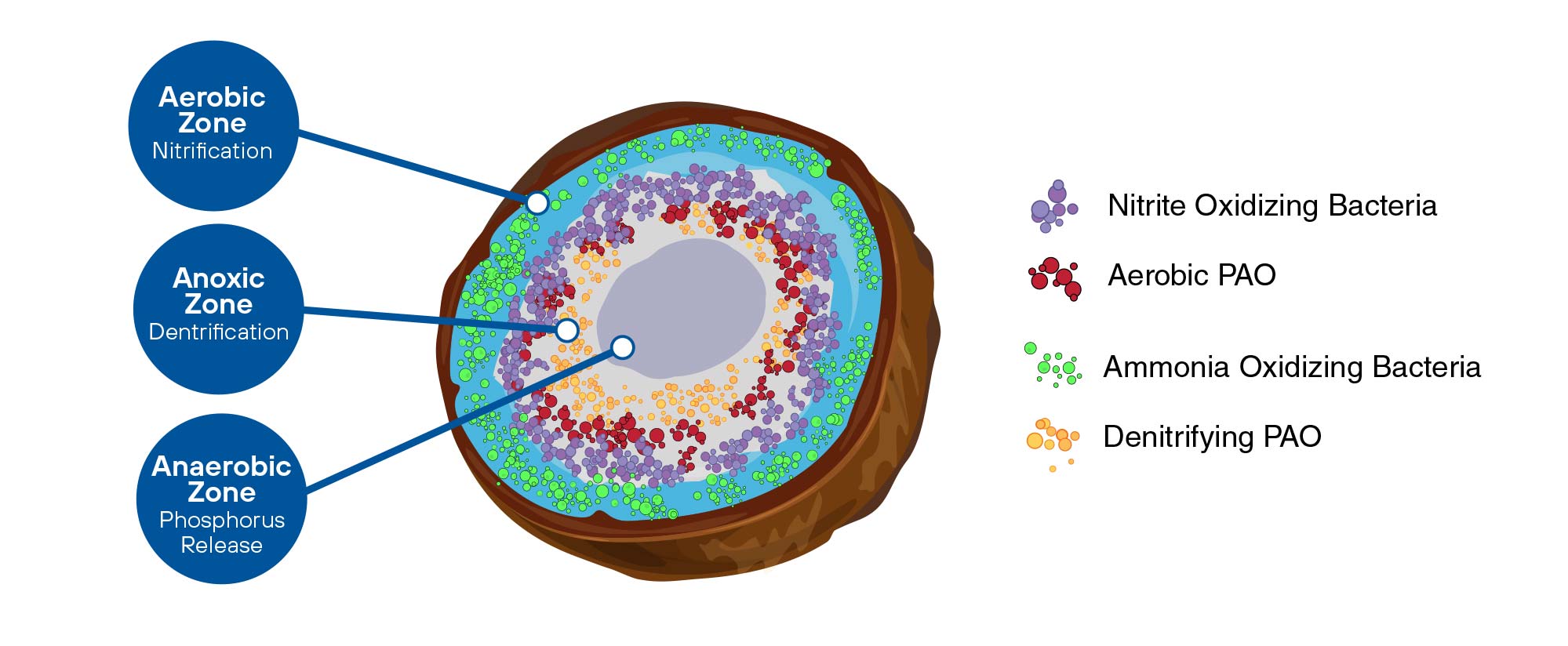
Multiple microbes growing in a single colony (granule) inherently have a higher density which results in a much higher settling velocity and sludge compaction when compared to typical activated sludge. The Granite AGS process typically achieves Sludge Volume Index (SVI) values of <50 ml/g. Keys benefits of the Granite AGS process include:
- Installation cost-saving due to smaller tank requirements. Systems can be designed at MLSS concentrations up to 8,000 mg/l.
- Less energy is consumed due to the reduced mixing needed for smaller basins.
- Process reliability greatly improved with rapid settling and compaction of <50 ml/g SVI.
- Reduced chemical consumption resulting from BNR occurring in the same colony.
The AGS process completes all unit process treatment steps within the reactors, eliminating the need for anaerobic or anoxic zones, RAS systems, and secondary clarifiers. Treatment occurs in four (4) steps:
ANAEROBIC FILL
The Granite tanks are typically operated in series with one tank being filled at any given time. Anaerobic fill occurs during the Filled Decant and Anaerobic Fill steps. During fill, the influent valve is opened allowing raw influent to enter the basin. No aeration occurs during this period so anaerobic conditions are present to encourage the production of ExtraCellular Polymetric Substances (EPS). EPS is a key component in the densification process that creates granular sludge particles. Oxygen Reduction Potential (ORP) is closely monitored during the anaerobic step to create the most favorable conditions for granulation.
REACT
Once the Granite reactor reaches the top water level or the designated anaerobic fill time has been reached, the flow will be diverted to another basin. Aeration and mixing occur in the reactor until complete biodegradation of organics has occurred. Since no flow enters the basin during react, no short-circuiting of raw, untreated waste can occur. Dissolved oxygen (D.O.) is typically monitored during the react phase to determine when residual D.O. starts to form, indicating that oxygen demand for the batch has been satisfied and treatment is completed. Luxury uptake of phosphorous also occurs during the aeration step.
Surface wasting of mixed liquor typically occurs during the React step. Waste sludge is transferred from the Granite reactor to the sludge thickening tank.
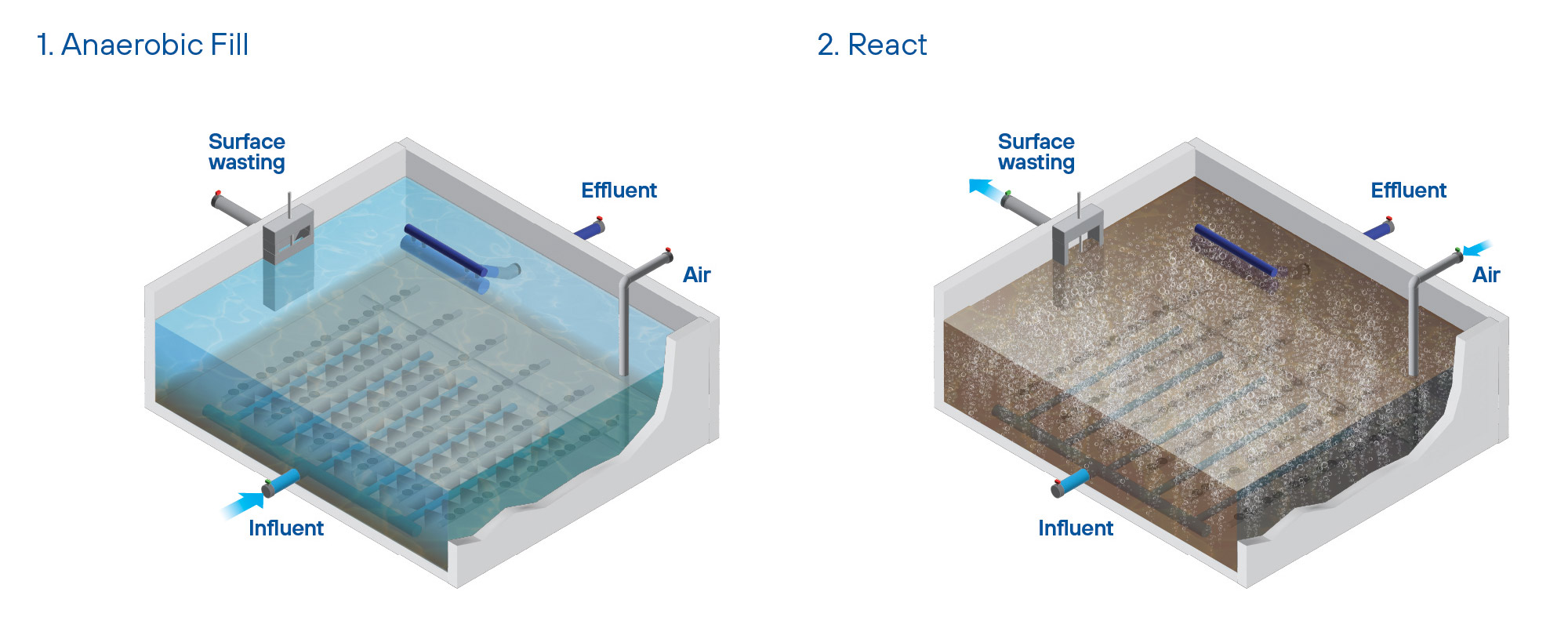
SETTLE
Following react, the Granite reactor will begin a settle mode in which liquids/solids separation occurs. No influent enters the basin during this period allowing for a perfect quiescent condition. All of the reactor volume is used for solids separation. The settling period typically lasts for 30 minutes but is field adjustable through the operator setpoints.
FILLED DECANT
The effluent withdrawal (Decant) begins once the settling period is finished. A floating decanter is used to maximize the interface between the withdrawal ports and the settled biomass. Typical systems will have roughly 30%-40% of the basin contents removed from the upper portion of the reactor during the decant period. Anaerobic fill also occurs during this step. An influent distribution system is utilized to allow low inlet velocities into the basin so the sludge blanket remains compact in the lower portion of the reactor during decant.
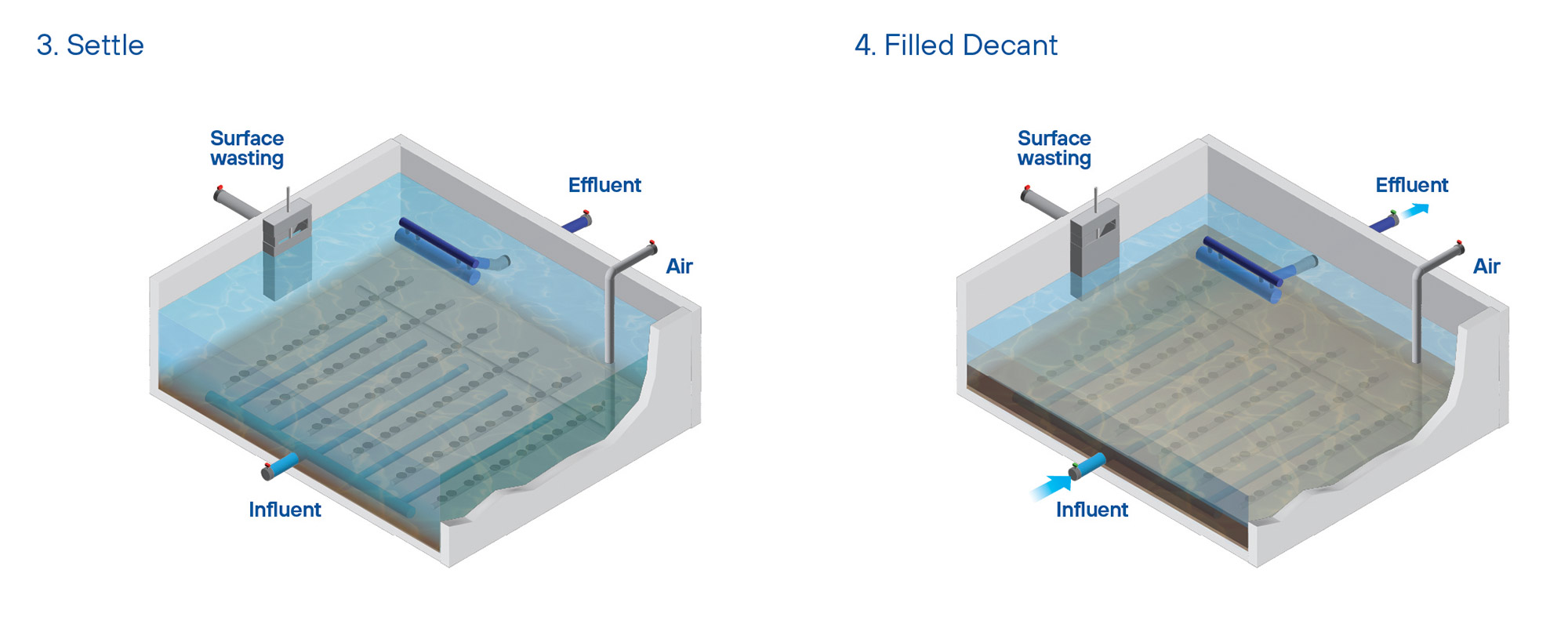
Granite AGS systems can be used in any secondary treatment applications. Primary markets are plants with stringent nutrient removal requirements, limited footprint, and a strong focus on low long-term cost of ownership. Retrofits of existing SBR or other activated sludge plants are also available.
For additional information on Granite AGS™ contact:
WaveLink . 2023
- Letter from the President: Empowering Progress and Growth
- New Product Announcement: Introducing Granite AGS™ Parkson’s Aerated Granular Sludge system!
- Aftermarket: New things happening in Parkson’s Aftermarket Maximizing Value in Parts, and Services
- Schreiber to expand and grow our in-house manufacturing capabilities.
- Catching the wave: Parkson holds its National Sales Meeting
- WEFTEC 2023 - Parkson’s Customer Rooftop Hospitality Reception Was a Big Success!s
- Index